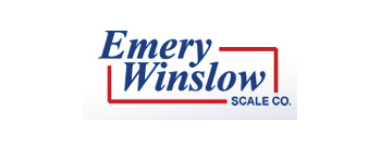
Infrastructure Needs Analysis Revitalizes Load Cell Production Flow Line
Emery Winslow Scale Company is a leader in the design, development, and manufacture of load cells, scales, and weighing systems and have been in business for 151 years. Their exclusive HydrostaticTM load cell technology allows the company to provide scales with both superior reliability and performance in the harshest environments, at the lowest cost of ownership.
Their scales are particularly resilient in tough environments where they may be exposed to water and power washing, lightning, corrosives, physical abuse, power surges, welding currents, and explosive conditions.
Over several decades, they have provided unique solutions to virtually every type of application for products of all kinds in a variety of industries, with extensive custom capabilities as well. Applications meet the requirements of a multitude of industries ranging from pharmaceuticals, food and chemical to transportation, waste and scrap.
Emery Winslow’s wide range of scale products include tank and hopper scales, floor scales, bench scales, truck scales, and railroad track scales.
Emery Winslow was interested in consolidating resources from a separate location into their Seymour, Connecticut facility where they would bring in load cell material to assemble, test, pack, and ship. Before making such a move, they needed to define the requirements of the move and consolidation. Specific and relevant criteria would have to be developed to help guide their decision to consolidate and implement such a move.
As part of Emery Winslow’s planned consolidation, they were looking to evaluate a viable “mixed model” production flow line capable of high and low volumes for their scales and load cell products and generate additional output. The company engaged the services of CONNSTEP to assist in reaching their stated goals.
Emery Winslow leadership discussed their stated goals and intentions with CONNSTEP who recommended a two-phased approach to determine the feasibility of a consolidation move and its subsequent implementation.
Phase 1 involved planning, defining flow line and developing a timeline of action items to help determine if the company would move forward with the consolidation. This included outlining improvements to make, refining processes, comparing current state to how to run future state, and a comprehensive plant layout. Scaled drawings of production floor plans were created as well as an inventory management process, WIP and a finished goods storage plan.
Phase 2 involved working with contractors and making adjustments to the final plant equipment layout and floor space. CONNSTEP also assisted and trained the Emery Winslow workforce on the mixed model production flow line the company was seeking to implement by defining workstation logistics and working with them to compile a list of equipment, tools and fixtures for each of the workstations within the flow line.
Emery Winslow’s fully operational flow line met their goal of providing high and low volume production of their scales and load cell products and have doubled their output since the consolidation. Workstations are compliant with the production velocities and processes required to meet demand and position the company to handle future growth.
The company continues to meet customer demand and is poised for business growth in large part due to implementing 5S and safety measures, streamlined work flow, lean techniques, visual mapping, inventory in the right place and having the tools and equipment they need. All leading to better productivity, inventory control, quality, and delivery.
Our whole concept improved with the help of CONNSTEP. We’re well positioned to expand and grow into new markets. This project eliminated any bottlenecks and set us up on the right course.
Dave Kelly - Vice President, Operations Emery Winslow Scale Company
Project Impact
Want to achieve results like these?
Related Items
Continuous Improvement Champion Certification (CICC)
This course provides comprehensive exposure to the principles and practices needed to develop and sustain a Lean Enterprise. You will receive immediate reinforcement of the classroom learning by applying your training to a real-life project within your organization.
[Case Study] Lean Manufacturing Improvements Result in Productivity Gains
IHCO was seeking to use their knowledge of the value of Lean continuous improvement to achieve productively gains in their order fulfillment processes and contacted CONNSTEP for assistance in reaching their goals.
Continuous Improvement Solutions Applied to Your Unique Needs
Implementing appropriate continuous improvement tools can help establish a Lean culture throughout an entire organization and deliver transformative results.