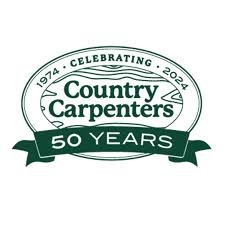
5S Implementation at Workstations Improves Production Flow
Country Carpenters designs and manufactures custom barn kits for customers throughout the United States. Based in Hebron, Connecticut, the company was founded in 1974 and has preserved centuries-old trade skills of post and beam construction that serve a variety of needs and interests.
Country Carpenters offer a range of structures, from garden sheds and carriage houses to small cabins and large country barns that combine the aesthetics of New England with the durability of post and beam. Their unique pre-cut, pre-engineered building kits ensure the integrity and durability of their high-quality products for years to come.
The management of Country Carpenters places a high level of importance on business growth and production efficiency. However, they faced the challenge of impending retirements of some long-time employees and the lack of familiarity of new hires with production workflow.
The supervisors at the company were skilled and tried to share their knowledge with the less experienced workers, but each station had specific tools and steps to follow. Country Carpenters management saw an opportunity to streamline each process and help everyone learn the best practices for a job, especially at their workstation.
Country Carpenters decided to partner with CONNSTEP to learn about Lean principles, tools, and techniques. The goal was to find continuous improvement opportunities within the organization and create a more efficient and streamlined workflow, and in turn, improve production efficiencies.
The production crew, owner, and managers participated in a lean awareness training workshop, where they learned about the many benefits of a Lean manufacturing enterprise. CONNSTEP also conducted a Value Stream Mapping (VSM) exercise with the production manager and key employee stakeholders at Country Carpenters to identify and eliminate bottlenecks and wasteful procedures in their production operations.
Lean techniques and processes implemented at Country Carpenters positively impacted all workers at the company. The most noticeable improvement was the 5S focus, which helped to organize and properly label the tools, parts, and materials at each workstation. This resulted in creating more streamlined, time-efficient deliveries, and ensuring quality standards.
The ideas generated by the employees during the VSM exercise that helped to identify and alleviate bottlenecks in the production cycle also established an improved use of layout space at each station.
“Thanks to CONNSTEP we learned a better way to improve production and workflow at our workstations. 5S has made the biggest difference, making us more organized and efficient. Labeling in work areas has been a big help, creating easier access to needed tools and eliminating wasted time.”
Josiah Loye, Chief Operating Officer, Country Carpenters