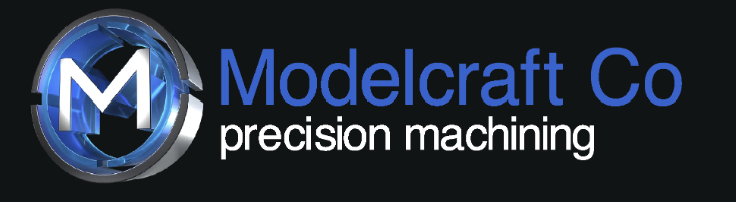
Continuous Improvement Measures Reduce Set Up & Inspection Time
The Modelcraft Company, which began operations in 1965, manufactures precision-machined parts for the medical, aerospace, and commercial industries at its facility in Plymouth, Connecticut. President and CEO Richard Merlino assumed ownership of the company in 2022 and was joined by co-owner David Hill the following year.
The talented employees at Modelcraft perform milling, turning, grinding, EDM, and assembly, primarily on aluminum and stainless steel materials. The company is AS9100D and ISO 9001:2015 certified. As a contract manufacturer, Modelcraft carries inventory and works according to customers’ forecasts, ensuring parts are delivered only as needed.
Modelcraft leadership made the decision to incorporate Lean manufacturing techniques and practices into their business processes to improve operational and financial performance, specifically looking for ways to increase the productivity of their milling department.
CONNSTEP recommended a PRIME (Process Re-engineering for Increased Manufacturing Efficiency) project, which is a Lean manufacturing process engineering study funded through the Connecticut Energy Efficiency Fund and administered by Eversource Energy. PRIME assists manufacturers in implementing process improvements that result in increased productivity and electrical energy efficiency.
CONNSTEP collaborated with a team at Modelcraft to assess their production operations and identify manufacturing processes that could reduce set up time and first piece inspection time. Their efforts also focused on identifying areas of waste in the production flow that contributed to delays in changeover time.
The cross-functionality of the Modelcraft team led to their inputs for improvement which provided greater production value. They diligently documented and measured the current and future states of their changeover process and its inefficiencies. They identified 12 no-cost or low-cost solutions to streamline material flow within the changeover process and to shorten changeover time, resulting in increased capacity and productivity of the milling department.
Modelcraft achieved several objectives, including a 15% increase in overall output from the milling department, shorter cycle time per part, improved material flow, and reduced changeover time. They also invested in new vision system equipment to enhance product quality and reduce waste.
Their continuous improvement efforts led to the creation of a new tool crib department, where tools were properly set up for easy access and reuse, leading to an improvement in quality. They also reorganized their lathe tool kits for greater efficiency.
“The biggest lesson we learned from this project is the importance of employee engagement. As more employees became involved, they saw the benefits of the improvements firsthand. They enjoyed sharing ideas, being heard, and seeing their suggestions implemented. It was a rewarding experience for everyone.”
Rich Merlino, President & CEO, Modelcraft Company