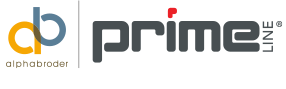
Lean Leads to Significant Production Efficiency Increase
Prime Line® has been a leading supplier in the promotional product industry since 1980, offering more than 1,600 items in 15 product categories. Its products are sold primarily in North America through a network of distributors.
The company markets promotional items such as bags, drinkware, writing instruments, apparel, stationery, gift sets, novelties, and more. In 2017, the company merged with alphabroder, the largest supplier of imprintable apparel in North America.
Prime’s business was surging and it was necessary for the company to improve the productivity of its pad printing department. Printing is a key form of revenue for the company and they wanted to grow without having to buy new machines or needing to hire more people.
Their goal was to increase efficiency by a minimum of 10%. Prime Line® turned to CONNSTEP, who they had worked with in the past, for training in Lean manufacturing tools and techniques to help reach their goal.
CONNSTEP met with the Prime Line® production team, reviewing the challenges they faced on a daily basis in the pad printing area, such as reducing machine downtime for improved productivity. Also, they expressed their desire for greater employee engagement in the production process for better company morale.
After initiating a Value Stream Mapping process and identifying areas of waste, the CONNSTEP team worked with key Prime Line employees on set-up reduction to help reduce the amount of downtime between production runs. CONNSTEP also introduced 5S to the production area for a less cluttered, more organized workplace and to be better prepared for next-in-line orders.
Applying set-up reduction to the pad printing process at Prime Line® resulted in reduced machine downtime, less material waste, fewer defects, and higher productivity. The ink, fixture and piece were ready to go, executing next-in-line orders more efficiently. The process was complimented by a 5S program that put materials in the right order for production purposes.
An incremental benefit was increased employee engagement and higher morale due to a sense of participation in and ownership of the new production process. Many solutions came from group leaders in different departments.
Prime Line exceeded their initial goal by increasing efficiency nearly 15%, turning out more products per day to meet their increased business demands.
Thanks to CONNSTEP we’re not wasting or scrapping. We’re working smarter and more efficiently which leads to greater savings that are shared with all employees. It’s a win-win situation for our company and employees, and for our customers. We’re able to ship a quality product and fulfill our mission of providing the ultimate customer experience.
Jerry Russo - Senior VP of Operations, Prime Line®
Project Impact
Want to achieve results like these?
Related Items
Continuous Improvement Solutions Applied to Your Unique Needs
Implementing appropriate continuous improvement tools can help establish a Lean culture throughout an entire organization and deliver transformative results.
Waste is plentiful in the manufacturing world, although much of it goes unnoticed, or at least unaddressed. If you’re thinking of waste purely in a physical capacity, you’re catching only a small glimpse of the bigger picture.
[Case Study] Lean Improvements Lead to Greater Order-Entry Efficiency
The leadership at Alden Tool recognized their operations were in need of some process improvements. They were aware the organization needed to become more efficient company-wide starting with order-entry.