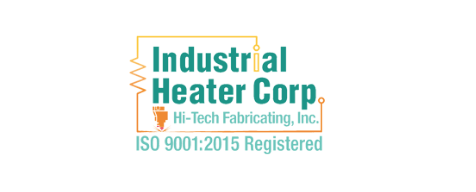
Lean Manufacturing Improvements Result in Productivity Gains
Industrial Heater Corporation (IHCO) designs and manufactures a wide variety of standard and custom heaters for industrial processing applications. An ISO-certified company known for their development and production of Band Heaters, IHCO has nearly 100 years of experience in the manufacturing industry with an exemplary international reputation.
A recognized leader in the process heating industry, the company is advancing its business with innovative design and quality products that build customer confidence and success.
IHCO has built its success by working with companies of all sizes and responding to customers’ needs by helping to keep their machines running smoothly and at optimum production levels.
Given the high cost of energy throughout the world, IHCO seeks to help their customers across many industries to control and reduce these costs in their operations. From Cartridge heaters to Autoclave Furnaces, IHCO products meet the needs for industrial processing.
Industrial Heater had worked diligently over the years to build a reputation for producing reliable, quality products backed by solid customer service and on-time deliveries.
Recently the company was experiencing longer lead times and delayed shipping. In addition, they were beginning to see a decline in information flow, excessive travel within office processes, and a lack of clear visibility to production requirements. All of which were increasing costs and inefficiencies.
As a result of these new developments, IHCO became interested in improving the productivity of their Mica and Sheet Metal (Hi-Tech) order fulfillment processes. Company leadership was well aware of the benefits of Lean manufacturing tools and techniques having previously participated in CONNSTEP’s Continuous Improvement Champion Certification program.
IHCO was seeking to use their knowledge of the value of Lean continuous improvement to achieve productively gains in their order fulfillment processes and contacted CONNSTEP for assistance in reaching their goals.
A CONNSTEP continuous improvement consultant met with the Industrial Heater team to review their challenges and discuss their goals and conducted a comprehensive process assessment of IHCO’s Mica and Sheet Metal (Hi-Tech) order fulfillment processes. The project was designated as a Process Reengineering for Increased Manufacturing Efficiency (PRIME) event funded by the local electric utility Eversource with execution and implementation by CONNSTEP.
The assessment process identified opportunities intended to have a positive impact on streamlining information and material flow with the Mica and Sheet Metal value streams.
Lean tools and techniques were taught to many of the IHCO workforce, introducing them to Kaizens, Standardized Work, 5S Visual Workplace, Kanban stations, and the overall benefits of streamlining product flow and eliminating or reducing waste.
CONNSTEP documented and measured the current state of the Mica and Sheet Metal process value stream. They also identified improvement opportunities towards building a future state value stream for each process with less waste and prepared an action plan to realize the future states.
Kaizen objectives for the Mica cell and Sheet Metal cell included:
- Create capacity to increase the overall output of the value stream
- Improve information and material flow
- Reduce overall lead time and cycle time
- Improve the First Pass Throughput Rate within material flow
CONNSTEP assessed the current situation and identified common problems being experienced by Industrial Heater for both their Mica cell and Sheet Metal cell:
- Completeness and Accuracy issues with incoming purchase orders
(Mica) and Request for Quotes (Sheet Metal) - Excessive Work in Process throughout the value stream resulting in longer lead times
- Lack of workplace organization
- Lack of alignment on multi-line orders resulting in delayed shipments
- Excessive travel and wait time among process steps
- Lack of clear visibility to production requirements
The kaizen resulted in the following improvements for each cell:
Mica Cell
- Number of process steps within the value stream decreased from 40 to 25
- Average Total Lead Time decreased from 18 to 8 days per order
- Average Total Process Time decreased from 126 to 76 minutes per order
- First Pass Throughput Rate per order increased from 1% to 25% and continues to improve
- Average Total Distance per order decreased from 754 to 574 feet
Sheet Metal (Hi-Tech) Cell
- Number of high-level process steps within the value stream decreased from 13 to 11
- Total Production Lead Time (Quoting to Shipping) decreased from 53 to 37 days per order
- Total Production Lead Time from Engineering to Quality Control decreased from 21 to 8 days per order
- Average Travel Distance per order decreased from 2,050 to 1,650 feet
We found the value stream mapping exercise very beneficial, putting pen to paper to quantify processes, evaluating them with actions to tackle them, and giving us a fresh approach.
Tom McGwire - Vice President, Business Development, Industrial Heater Corp.
Project Impact
Want to achieve results like these?
Related Items
Often basic housekeeping is overlooked in favor of “productivity.” This is a common practice but one that costs you over the long run. Putting a basic 5S program in place is inexpensive and yields a great return on your (small) investment.
Continuous Improvement Champion Certification (CICC)
This course provides comprehensive exposure to the principles and practices needed to develop and sustain a Lean Enterprise. You will receive immediate reinforcement of the classroom learning by applying your training to a real-life project within your organization.
[Case Study] Enterprise-Wide Lean Transformation Drives Growth & Revenue
“The enterprise-wide lean transformation facilitated by CONNSTEP helped give us the continuous improvement head start we needed."