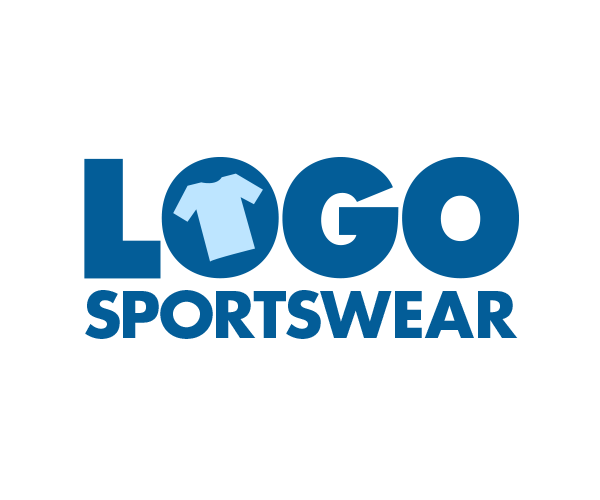
Streamlined Tracking System Expedites Production Turnaround Time
LogoSportswear is a premier supplier of custom branded apparel and promotional items. Located in Wallingford, Connecticut, the company has been providing a wide selection of made-to-order attire that includes custom shirts, caps, workwear, team jerseys, as well as promotional products, for organizations and events since 1995.
They utilize state-of-the-art digital printing and embroidery equipment and technology to produce their logo branded apparel and promotional merchandise. LogoSportswear is a subsidiary of Digital Room – a company capable of producing an impressive breadth of marketing and branding materials through a collection of more than a dozen ecommerce sites.
The leadership team at LogoSportswear wanted to improve order processing times and was seeking to identify new data management and tracking solutions. Their vision was to accelerate the customer buying process by developing and enhancing their order location tracking system with the goal of building value for both the organization and the customer.
Logoworks is the customized enterprise resource planning (ERP) system used by LogoSportswear for their core business processes. Leadership was interested in leveraging their ERP to manage the barcoding within the tracking system, and to create a mobile app for different handheld devices in support of accelerating order completion, especially during their peak holiday season.
In order to determine the most efficient process to get more orders out the door, LogoSportswear turned to CONNSTEP, their local MEP center, for assistance. CONNSTEP engaged their partner Triple Helix Corporation (3XC) to conduct a data management/process review for LogoSportswear.
To ensure the best outcome of any development efforts, 3XC conducted an assessment with all key stakeholders to understand and evaluate how data is being managed across the company, between departments, and with major clients. Discussions were held with purchasing, production, sales, customer service, finance, back office, and senior leadership at LogoSportswear.
A comprehensive internal review was completed of current workflow challenges, waste, and opportunities, focusing on driving faster turnaround time in production and reducing the time orders are on hold and sitting on a shelf.
A prioritized plan was delivered that addressed process and production issues, along with detail on off-the-shelf software/hardware solutions and custom-coded enhancements to existing Logo Sportswear systems which the company opted to implement, based on existing technology within the Digital Room enterprise.
CONNSTEP and its partner Triple Helix helped LogoSportswear achieve our vision. Internal teams saw the value in the process, enabling us to open up areas for improvement, create an enhanced order location tracking system, and lead us to make significant capital investments in equipment, all in support of delighting our customers.
Ralph Pantano, LogoSportswear, Inc.
Project Impact
Want to achieve results like these?
Related Items
Often basic housekeeping is overlooked in favor of “productivity.” This is a common practice but one that costs you over the long run. Putting a basic 5S program in place is inexpensive and yields a great return on your (small) investment.
Waste is plentiful in the manufacturing world, although much of it goes unnoticed, or at least unaddressed. If you’re thinking of waste purely in a physical capacity, you’re catching only a small glimpse of the bigger picture.
Continuous Improvement Champion Certification (CICC)
This course provides comprehensive exposure to the principles and practices needed to develop and sustain a Lean Enterprise. You will receive immediate reinforcement of the classroom learning by applying your training to a real-life project within your organization.