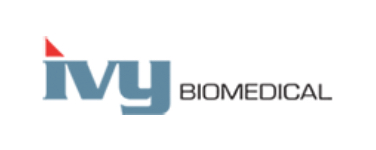
Value Stream Mapping Leads to Medical Device FDA Success
Ivy Biomedical Systems is an industry leading medical device manufacturer focused on cardiac and respiratory gating solutions. Located in Branford, Connecticut, all of its products are designed, developed and manufactured here.
The privately-held company has sold over 60,000 trigger monitors and modules since its inception in 1984. They are the market leader for precision gating monitors used for synchronization of radiographic image acquisition across all major modalities.
Their primary OEM partners include GE Healthcare, Hitachi Medical Corporation, Philips Healthcare, Siemens Medical Systems, and Toshiba Medical Systems. Assistance is provided to these OEM partners with product registrations in over 180 countries worldwide.
Ivy Biomedical was facing a Food and Drug Administration (FDA) mandate to implement the UDI Rule which establishes a unique device identification system for medical devices. Under the rule, the healthcare community and the public will be able to identify a device through a Unique Device Identifier (UDI) that will appear on the label and package of a device. The UDI will provide a standardized way to identify medical devices across all information sources and systems, including electronic health records and devices registries.
In order to meet the UDI requirements mandated by the FDA, Ivy Biomedical needed a uniform system that would standardize their methods and provide alignment of the build structure to implement the system. An efficient process was necessary to avoid adversely affecting the company as they prepared to design and develop UDI labels universally across all products.
Having worked with Connecticut’s MEP center CONNSTEP in the past, the executive leadership at Ivy Biomedical turned to them again for recommendations to clarify and optimize the process to meet UDI requirement of the FDA mandate.
To assist Ivy Biomedical meet FDA requirements for implementing a UDI system and continue to produce monitors, CONNSTEP recommended a PRIME (Process Reengineering for Improved Manufacturing Efficiency) project.
A key component of the PRIME project involved Value Stream Mapping of both their manufacturing and service department areas. In their manufacturing area, the mapping helped Ivy structure the “U” in UDI which is the point in which a monitor becomes Unique, or customer-specific, such as for GE or Siemens.
In their service area, the mapping process allowed Ivy to understand how to handle field returns for those devices, both with new UDI requirements and those with pre-UDI requirements. It created a process that included decision points for UDI and pre-UDI directives.
The value stream mapping tool was an instrumental part of helping with their adoption of the UDI Rule. In mapping out its value stream, Ivy Biomedical brainstormed on ways to identify where to implement UDI – at which stage in the process it would be most efficient. It also helped them to pinpoint weaknesses in the label generating process.
The PRIME project recommended by CONNSTEP allowed Ivy Biomedical to successfully implement the FDA mandated UDI Rule establishing a unique device identification system for medical devices. It resulted in the alignment of the build structure to accept the UDI and avoided negatively impacting the company had they not done it.
By mapping out the manufacturing process to introduce and implement the UDI system, Ivy Biomedical was able to invest in the necessary infrastructure to meet the FDA requirements, helping to protect and retain sales and save jobs. Additionally, it allowed the company to understand how to handle field returns.
CONNSTEP opened up our eyes to see where we can assign the UDI in the manufacturing process and get it to the finished level. The Value Stream Mapping clarified the process for us to help meet UDI requirements mandated by the FDA. It all resulted in being able to make appropriate investments and implement a successful UDI system.
Zack Curello - Vice President/General Manager Ivy Biomedical Systems
Project Impact
Want to achieve results like these?
Related Items
Continuous Improvement Solutions Applied to Your Unique Needs
Implementing appropriate continuous improvement tools can help establish a Lean culture throughout an entire organization and deliver transformative results.
Waste is plentiful in the manufacturing world, although much of it goes unnoticed, or at least unaddressed. If you’re thinking of waste purely in a physical capacity, you’re catching only a small glimpse of the bigger picture.
[Case Study] Value Stream Mapping Helps Reduce Lead Time
“After evaluating our mold making process and identifying improvement opportunities, we’ve significantly reduced our overall lead time and improved first pass yield. With our improved workflow, we’re able to get jobs out quicker.”