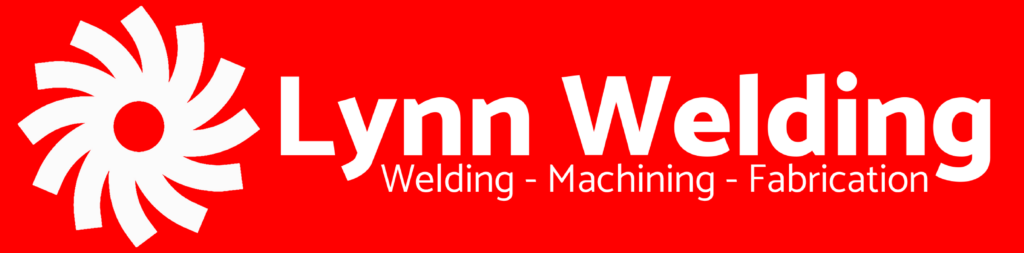
Visual Management Tools and Set-Up Reduction Drive Quality and Production Gains
Lynn Welding is an industry leader of welding and machining for the Aerospace, Defense, Nuclear, Industrial, and Medical industries. The company started in 1979 as a one-man shop with a Tig welding machine. Named after the original owner’s daughter, company ownership changed hands in 2007. The business is located in Newington, Connecticut.
The ability to weld, machine, and fabricate entire assemblies is what differentiates Lynn Welding from the competition. The company holds an extensive list of qualifications from a broad list of customers and is highly respected within the aerospace community when it comes to producing X-Ray quality welds. Customers consider Lynn Welding the ultimate solution for complex welding and machining.
The management of Lynn Welding identified areas of opportunity for improvement including the high cost of finished goods inventory, longer than desired lead times, decreased capacity, and the challenge of sustaining lean initiatives.
The issues in these areas have led to lower on-time deliveries, higher overtime costs, and an excessive number of expedited orders. Lynn management turned to CONNSTEP for help in streamlining processes to improve quality, cost, and delivery as well as establishing and replicating best practices across the company.
CONNSTEP recommended a two-phase approach, which included Value Stream Mapping (VSM) of a fabricated product family and coaching kaizen teams.
CONNSTEP conducted a VSM exercise which identified current steps and sequences followed in one of Lynn Welding’s fabricated products. It also highlighted external quality issues, such as incomplete order information, and some internal issues, which needed greater attention.
The Lynn team used the current state value stream map to identify areas of improvement. Coaching of the Lynn Welding implementation teams was done to help them build towards a streamlined future state.
A CONNSTEP consultant also worked on set-up reduction principles focused on creating standardized work procedures for one welding booth and then applying the standardization to Lynn’s other welding booths.
The VSM looked at a key fabricated product family and identified improvements that included 5S, visual management, and reducing batch size. Set-up reduction focused on welding and welding booth operations which was successfully applied to other booths within the organization.
These improvements resulted in:
- Production scheduling board – this became a visual tool that gave visibility into what was going on with the job, aligning what to work on now vs. what is in the pipeline
- Point of use storage – exposed any abnormalities such as not having the right tools or materials, ensuring whatever an employee needed to do their job was immediately available to them
- Welding Booth Standardization – resulted in better product quality, shorter set-up time, which translated to shorter lead times and greater efficiency
“We’ve really seen a culture of continuous improvement emerge with the mandatory use of visual boards. It’s become a habit to check the scheduling boards to help keep the jobs flowing. It’s now our standard way of operating.”
Ibrahim Ibrahim, Lynn Welding Company, Inc.