5S System Improves Workplace Organization & Productivity
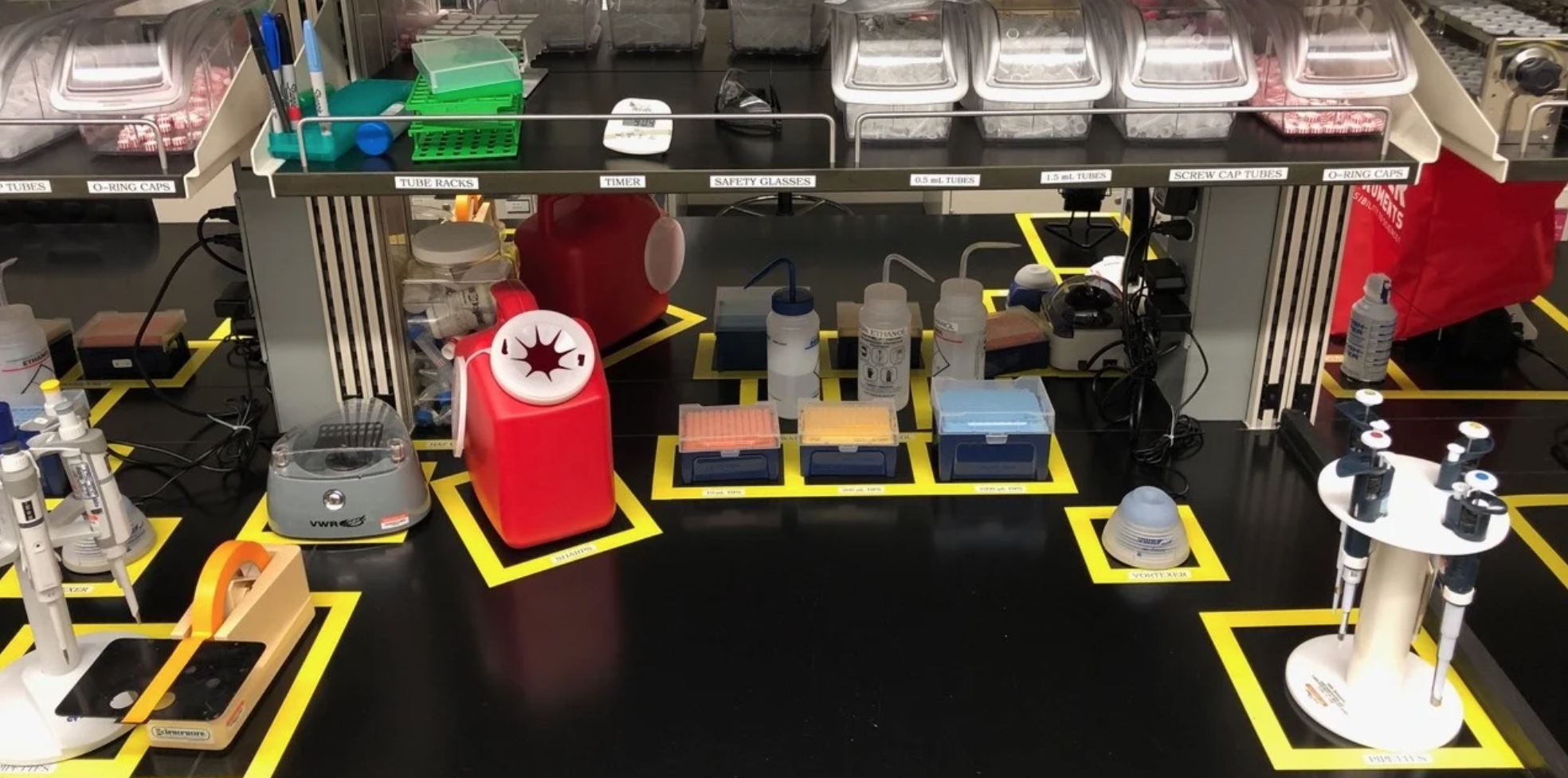
In a manufacturing production environment, having an organized and orderly workplace leads to better flow and greater efficiency and often allows workers to produce more at a sustained rate.
The 5S’s are action steps that begin with the letter S: Sort, Set in order, Shine, Standardize, and Sustain. Key team members should weigh in to create consensus when addressing each “S” in the process.
Let’s look at each step individually:
Sort
The purpose of the Sort procedure is to review items, such as tools and equipment, which are used in production of a specific work area. Keep what is needed, add what’s missing, and remove what is not needed. Place a red tag on items not needed or in the wrong work area.
Set aside the items used every day at the work station and place the supplies you may need but don’t use regularly in a separate storage area where they are easily accessible.
Set in order
Once you have removed the unnecessary items from the workspace, it’s time to find a proper place for the necessary ones used regularly for production. In the Set in order process, you evaluate the efficiency of your current workflow. Review the steps and motions employees take to perform their work task along with the required tools and supplies.
Determine the most logical arrangement for the items you need, keeping in mind their frequency of use, ease of access and return. Safety is also a factor as well as eliminating wasted movement, reaching, and effort.
The use of visual cues is encouraged such as a map of the workspace showing where the equipment and tools are now located. From here, you can visually demonstrate the steps employees must follow to perform their assigned tasks for that specific area of production.
Shine
This step is the time to Shine which involves cleaning the work area and everything in it, eliminating all forms of contamination including dirt, debris, dust, and fluids. This is not just for the sake of housekeeping but to establish a new standard.
Also, inspect equipment to look for wear and tear that might lead to its failure during use. This should essentially be done every day along with daily cleaning to ensure the best operating condition of the tools and equipment and to replace or repair anything that needs it.
Standardize
In this step, you Standardize the first three S’s in 5S by developing rules to maintain them. Rules should focus on locations of things in the workspace, position of items in the work area, amount of supplies required for the production task, cleaning schedules, and procedures to do the job.
Once you have standardized procedures within the designated work area, document them using visual mapping cues to establish standards that are easy to follow and understand. The standards help ensure that 5S becomes an essential part of daily work and enables workers to manage and control their area.
Sustain
This step is where you Sustain the gains made implementing the methods of the four previous steps. The best means to make this happen is to stick to the rules and procedures. This will lead to new, daily habits that will facilitate productivity and create more consistent quality.
Familiarize employees with visual management techniques, properly train them, and ensure the leadership of the organization is committed to the program’s success.
The benefits of utilizing the 5S system are numerous, including work standardization, reduction in cycle time, decreased changeover time, better quality and greater safety. A gratifying side effect of the 5S system is that it may also improve employee morale.
Related Items
Often basic housekeeping is overlooked in favor of “productivity.” This is a common practice but one that costs you over the long run. Putting a basic 5S program in place is inexpensive and yields a great return on your (small) investment.
[Case Study] Enterprise-Wide Lean Transformation Drives Growth & Revenue
The company tasked itself to grow the business with current resources by becoming more efficient, reducing waste, and developing more productive internal capabilities.
Continuous Improvement Champion Certification (CICC)
This course provides comprehensive exposure to the principles and practices needed to develop and sustain a Lean Enterprise. You will receive immediate reinforcement of the classroom learning by applying your training to a real-life project within your organization.