4 Steps to Improve On-Time Delivery with Production Schedule Management
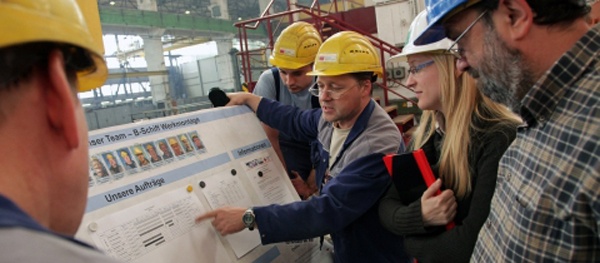
Reliable delivery performance is what every manufacturer strives for and what every customer expects. By improving your delivery performance metrics, you not only increase customer satisfaction but also increase the odds of keeping existing business and growing new business opportunities. These four steps can help you achieve this goal:
1) Small Intervals in Lean Production
Any improvement initiative must involve the person responsible for planning and scheduling from the outset. Traditional manufacturing processes are usually designed to handle big batches and typically focus on scheduling over long periods, such as one month out.
Lean manufacturing shifts the focus in scheduling and planning production to the near term. The reason for this is that the closer your manufacturing processes are tied to meeting defined customer needs, the better chance you have of meeting the production schedule expected by your customers.
The goal is to optimize your production schedule relative to timing and mix and to bring it down to the smallest interval. It’s a very different approach from past efforts to optimize production schedules by running large batches.
2) Shorter Measurement Intervals for Faster Troubleshooting
Lean thinking focuses on producing the right quantities at the right time for your customers, utilizing your resources to shorten lead times, and continuously meeting your promises.
Your ability to know at any given moment whether your production schedule is meeting customer expectations gives you the advantage to meet changing customer demands. But measuring whether your production schedules worked at the end of the week or month is not enough, you should measure them continuously, even hourly if possible.
Things will occasionally go wrong, and you may wonder, won’t a shorter measurement interval compound the problem? The key is that with production schedules managed to small time frames, such as hourly if possible, you can react faster to solve production problems as they arise, helping to stay on track with customer demand. Having a skilled organization with effective problem solving abilities will ensure proper management of this information.
3) Discover Where Your Schedule Should Begin
Applying Lean thinking to your production processes will identify the one area that is the slowest point in your operational flow. This area of constraint is also an important control point for your scheduling.
We refer to this point as “the pacemaker,” and it’s from this point you should schedule. In reality, the pacemaker point controls what happens through the rest of your processes, setting the overall speed of product flow or product pull.
To determine the optimized production schedule that shortens your lead times, we first calculate a time interval for “Every Part Every Interval” or EPEI. This value is based on your quality levels, times required for machine setup, the production cycle itself, and the operating performance of the machinery (machine utilization). The EPEI ultimately helps you establish your planning horizon for your product mix.
4) Establish the Right Metrics
Some companies may schedule by gut instinct or experience. For example, you may be used to your schedule routine being two weeks, yet Lean manufacturing tools could cut it to eight days. How much capacity would that free up, ready to be filled with new business? Or what impact might this have on shortening lead time or increasing on-time delivery performance?
While a master production schedule gives you a broader outlook, you also need to be looking at the schedule more in real-time, with shorter EPEI’s, which will enable you to always know where you are in your schedule on a real-time basis. It requires a thorough understanding of your capacity as well as the management of resources creating that capacity – your equipment and your employees.
The right metrics help you understand where you are relative to meeting the schedule in real-time. It’s simply not sufficient to release a schedule for the week and then check against it at the end of the week. Understanding where you are in the schedule should be a dynamic process that is continually monitored against the proper metrics. Utilizing a visual schedule board will give you immediate and real-time information on the status of actual to plan.
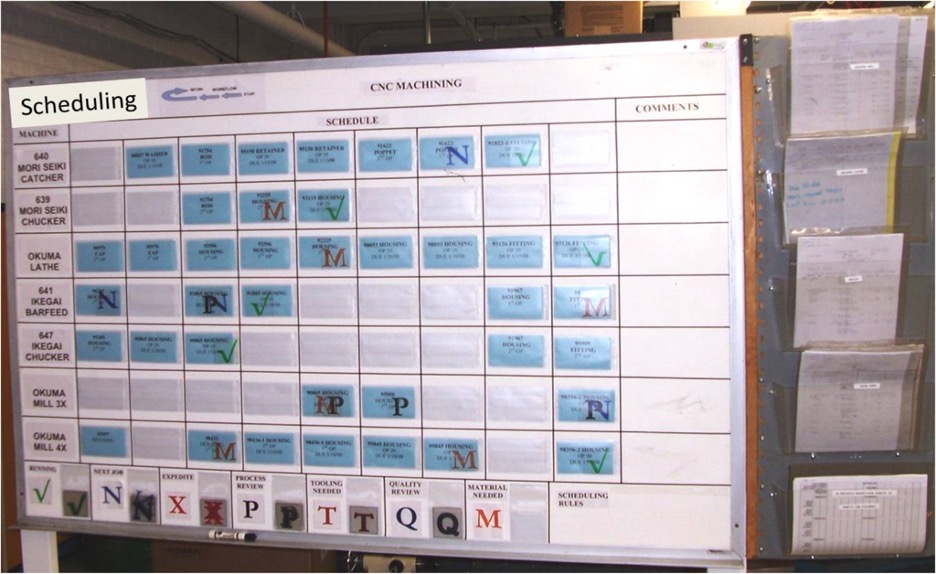
Not everyone needs to be involved in production scheduling, but the right people must be part of your Lean manufacturing initiative. The outcome of managing the plan correctly will be improved performance, greater on-time delivery, and increased customer satisfaction – the winning trifecta of driving overall business growth.
Related Items
Establish a Culture of Quality
CONNSTEP specialists work with you every step of the way applying their years of experience in quality management systems consulting and process improvement services to help you meet your goals.
CONNSTEP’s Quality Essentials Program is being offered to address the growing need to enhance the knowledge of quality principles among skilled manufacturing workers.
[Case Study] Strategic Roadmap Brings Synergy to Growth and Operations
Corru-Seals recognized to fully realize the benefits inherent in the new quality standard would require a paradigm shift in the organization.