Preventative Maintenance Keeps Your Business Running Smoothly
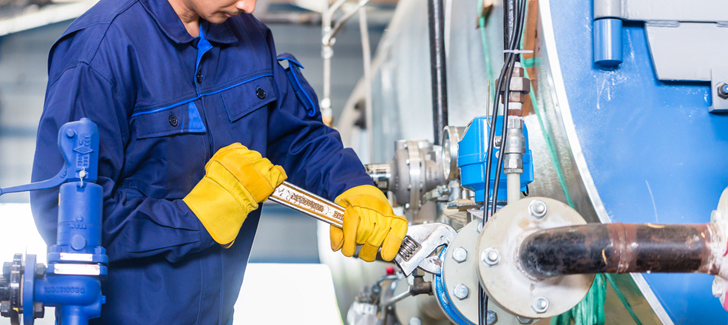
We’ve all heard the motto, “if it’s not broke, don’t fix it.” It’s an approach that may save a company money in the short term but can often end up costing even more in the long run.
For manufacturers that rely on production equipment and automation for their business, this type of “wait and see” maintenance strategy is referred to as “reactive maintenance.”
On the other hand, when a company follows a strategy where they routinely perform scheduled maintenance tasks in order to avoid larger, more costly fixes down the road, it’s considered “preventative maintenance.”
There are many benefits to the ongoing equipment upkeep of preventative maintenance versus reactive maintenance. Here are some key reasons for properly maintaining equipment and automation at your facility:
Cost Savings
A preventative maintenance plan focuses on avoiding equipment failure rather than responding to emergencies, and catching small service issues before they become bigger repair headaches.
Manufacturers that are reactive with their maintenance needs are essentially waiting for a problem to happen which can be a costly proposition. Unplanned downtime can result in unproductive employees, interrupted workflow, missed deadlines, and potentially compromised customer relationships.
Unexpected breakdowns may also result in having to pay repair technicians overtime and incur expenses for rush delivery of needed parts. Much of which can be avoided with a preventative maintenance plan.
Equipment Efficiency
Planning routine maintenance of equipment and automation through inspections, worn part replacements, fluid changes, and regular cleaning allow shop floor operations to run much more efficiently. Consistent productivity is ensured with equipment operating at peak performance.
In addition, equipment that is serviced regularly does not have to be turned over, or replaced, as frequently lowering investment and upgrade costs over time.
Higher Reliability and Less Downtime
Virtually all maintenance tasks require some equipment downtime. A preventative maintenance program can decrease and optimize that downtime so it is less disruptive to the production of the business, saves time, and streamlines the day-to-day operation of the facility.
Preventative maintenance can also help a manufacturer be a more reliable business partner. It will ensure that it delivers its products, services or materials on time to its customers without unnecessary delays. This also enhances its customer service, improves its reputation, and differentiates its brand.
Improved Safety
Equipment failures can have catastrophic consequences. When machines are not in optimal shape, it can create hazards, a compromised work environment, and possibly situations where workers become injured.
Properly maintaining equipment will result in safer working conditions for the operator as well as those working nearby. Preventative maintenance not only improves the safety of equipment but may also result in fewer on the job injuries and accidents.
Prolonged Equipment Life
There are numerous benefits shifting from a reactive to a preventative maintenance program. The bottom line is that the better a company cares for its equipment and automation, the longer it will last.
Preventative maintenance will prolong the life of equipment enabling a business to get more hours and production out of it, leading to less downtime, reduced costs, and increased profits. It’s a smart move for companies to regularly schedule equipment maintenance to sustain their competitiveness and help them succeed in the long run.
For more information about reducing downtime at your business, contact CONNSTEP to schedule a no-obligation discovery meeting.
Related Items
Often basic housekeeping is overlooked in favor of “productivity.” This is a common practice but one that costs you over the long run. Putting a basic 5S program in place is inexpensive and yields a great return on your (small) investment.
[Case Study] Enterprise-Wide Lean Transformation Drives Growth & Revenue
The company tasked itself to grow the business with current resources by becoming more efficient, reducing waste, and developing more productive internal capabilities.
Continuous Improvement Champion Certification (CICC)
This course provides comprehensive exposure to the principles and practices needed to develop and sustain a Lean Enterprise. You will receive immediate reinforcement of the classroom learning by applying your training to a real-life project within your organization.