3 Things to Consider Before Pursuing ISO Certification
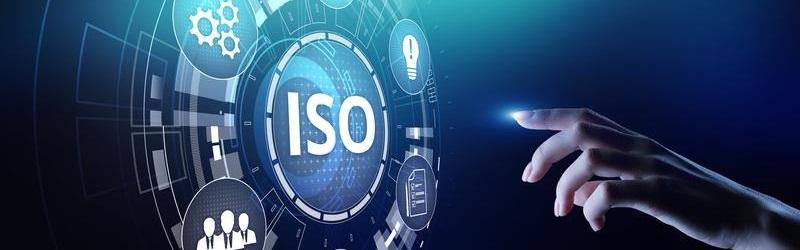
Quality is something every successful manufacturer incorporates into their business model. Customers demand it and your reputation relies on it. Some customers require that their suppliers or contractors have an ISO certificate in order to do business with them.
Achieving ISO standards are often what separates one company from the competition. And in many cases businesses have the opportunity of leveraging new market opportunities that they could not do business with before being ISO certified.
But before taking the steps to seek ISO certification for your business, there’s three considerations to address:
1. Certification is not an end in and of itself. It should be a part of what you do and should complement the other components of your overall business strategy.
It would be a mistake for any manufacturer to think if you achieve an ISO standard that great things will suddenly happen to your business. But when tied to your strategy, pursuing certain quality standards can make your company better at what it does, position it as a more attractive business partner, and help it reach its overall strategic goals.
It’s important to be purposeful and to understand what a new certification can, and can’t, do for our business. To know which ISO certifications your business can benefit from, first identify where and how you want to participate in your chosen marketplaces. For success, it’s critical to tie everything to your overall business strategy.
2. Standards should be used to improve your business processes. Certification should be seen as an opportunity to identify processes improvements that can create improved business results overall.
ISO standards attempt to ensure quality, consistency, and safety and show how to check for quality. ISO standards provide organizations with the knowledge they need to improve performance and optimize their operations. This will also result in more satisfied customers and facilitate the ability to identify and implement new working practices more efficiently and faster.
An ISO certification can take time and effort and may require improvements to some areas of your business.
Achieving certification to an ISO standard can result in increased sales and revenue. Implementing ISO standards demonstrates to customers, stakeholders, and employees your commitment to producing a quality, reliable product, and generates confidence in your offerings.
3. Certification will not get you more customers or improve your business on its own, although it may be a requirement to keep some customers. You’ll need a strategic business plan and an active marketing plan to maximize the benefits of that new certification.
ISO certification isn’t necessary in every case, often depending on how close your business is to producing a finished product in the supply chain. Generally speaking, the closer you are to the end product, the greater the need for quality certifications. It may also be contingent on your overall business goals and strategic direction of your company.
For example, smaller manufacturers that are farther down the line of a large supply chain may find that certifications are not necessary for their success. However, if one of your objectives is to grow business as a supplier to more manufacturers or to become a bigger player in the industry, pursuing the right certifications can be a smart strategic move.
Help in Achieving ISO Certification
When you’re closely invested in your company, sometimes it can be hard to “see the forest for the trees.” That’s why seeking assistance from a third-party can help you determine whether you should pursue a quality certification. Experienced quality consultants have a comprehensive understanding of the standards, as well as the ability to interpret what they truly mean and can apply them successfully to an individual business.
Consultants who are also registrar auditors understand what the registrars look for when auditing a company to determine if it’s compliant, and use their experience to help you avoid many of the pitfalls on the road to certification.
Download this infographic on why to consider ISO 9001 certification and its process.
Contact us if you’d like to learn more.
Related Items
Establish a Culture of Quality
Implementing appropriate continuous improvement tools can help establish a Lean culture throughout an entire organization and deliver transformative results.
CONNSTEP’s Quality Essentials Program is being offered to address the growing need to enhance the knowledge of quality principles among skilled manufacturing workers.
[Case Study] Strategic Roadmap Brings Synergy to Growth and Operations
Corru-Seals recognized to fully realize the benefits inherent in the new quality standard would require a paradigm shift in the organization.